General introduction
Polycrystalline Mullite Fiber (PMF) is a novel super-light high temperature refractory fiber in the world, one of the whole Al2O3-SiO2 system ceramic fibers, with use temperature of 1800 degrees to 1700 degrees, 200 degrees to 300 degrees higher that that of fiber glass.
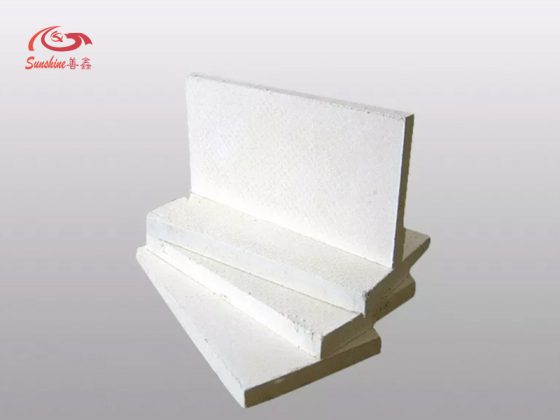
Polycrystalline mullite fiber (PMF) is currently at home and abroad the latest ultra-lightweight high-temperature fire resistant fiber, the whole system Al2O3SiO2 ceramic fibers in two different products, It can be widely used in metallurgy, machinery, electronics, ceramics, chemicals, aerospace and other high temperature industrial furnaces and other thermal equipment, lined with insulation.
In order to achieve energy efficiency increase, extend furnace life, the purpose of improving the working environment. Appearance white, smooth, soft, flexible, just like cotton.
Characteristic
It is characterized in white appearance, smoothness, softness and elasticity, just like pledget. PMF is a polycrystalline mullite fiber in the existing form of mullite crystalling phase, with a unique structure, complicated manufacturing process and high technical content.
- High temperature stability to 1600-1800C
- Ideal for use as furnace insulation in sintering, heat treating and chemical thermal process systems
- Non-Flammable
- Excellent thermal shock resistance
- Resistance to most chemical attack; it has excellent stability in acid metal slags and is insoluble in most acids
- Resistance to oxidation and attack by furnace atmospheres
- Resistance to abrasion
- Good electrical resistivity
- Excellent thermal stability
- Can be used as insulation packing in furnace spaces and around furnace sight tubes & ports
- Fill in expansion joints and masonry cracks inside of furnaces.
Different types
Ceramic fiber board | SS1050C-RBD | SS1260 ST-RBD | SS1260 HP-RBD | SS1350 HA-RBD | SS1430 Zr-RBD | SS1600 PCF-RBD | SS1700 PCF-RBD | SS1800 PCF-RBD | |
Max Service Temperature(℃) | 1050 | 1260 | 1260 | 1350 | 1430 | 1600 | 1700 | 1800 | |
Density (kg/m³) | 220/250/280/300/320/350/380/400 | 400/450/500/550 | |||||||
Linear hrinkage(%) (After burning)(24h) | ≤3.0 950℃ | ≤3.0 1050℃ | ≤3.0 1100℃ | ≤3.0 1200℃ | ≤3.0 1300℃ | ≤1.0 1450℃ | ≤1.0 1550℃ | ≤1.0 1650℃ | |
(MPa)Modulus of rupture | ≥0.3 | ≥0.4 | ≥0.4 | ≥0.4 | ≥0.4 | ≥0.6 | ≥0.6 | ≥0.6 | |
(%)Loss on ignition | ≤8.0 | ≤4.0 | |||||||
Thermal conductivity rate(W/m.k) | 400℃ | 0.08 | – | – | – | – | – | – | – |
600℃ | 0.12 | 0.12 | 0.12 | 0.12 | – | – | – | – | |
800℃ | 0.16 | 0.16 | 0.16 | 0.16 | 0.16 | 0.17 | 0.17 | 0.17 | |
1000℃ | – | 0.23 | 0.23 | 0.23 | 0.23 | 0.23 | 0.23 | 0.23 | |
Chemical Composition(%) | Al2O3 | ≥37 | ≥41 | ≥43 | ≥45 | ≥37 | ≥65 | ≥70 | ≥72 |
Al2O3+SiO₂ | ≥97 | ≥97 | ≥98 | ≥98 | ≥84 | ≥99 | ≥99 | ≥99 | |
ZrO₂ | – | – | – | – | ≥11 | – | – | – | |
Others | ≤3.0 | ≤3.0 | ≤2.0 | ≤2.0 | ≤2.0 | ≤1.0 | ≤1.0 | ≤1.0 | |
Standard size(L*W*T)mm | 1200/600*1000*(6-105),1200*500*(6-105) | 1000/900*600*20-150 | |||||||
Package | Cartons or Pallets | Wooden | |||||||
Other sizes of products and packages are available as required. | |||||||||
Recommended using temperature:In oxidizing or neutral atmosphere,100~250℃Recommended usingtemperature:In oxidizing or neutral atmosphere,100∽250℃lower than the maximum service temperature,In reductive atmosphere,200~350℃ lower than the maximum service temperature. |
Applications
- High temperature sealing gasket
- Anti-scour parts of lining inner paste
- Hot surface material of high temperature furnace lining
- Heating device thermal insulation
- Furnace door and body filling material