Why chooose alkali resistant coating SiC heater?
Alkali resistant coating SiC heater is also called “D coating SiC heater”, it can make SiC heater last longer.
SiC heater can be used in the furnaces with different atmospheres, however, service life of SiC heater will be affected and shortened under some atmospheres.
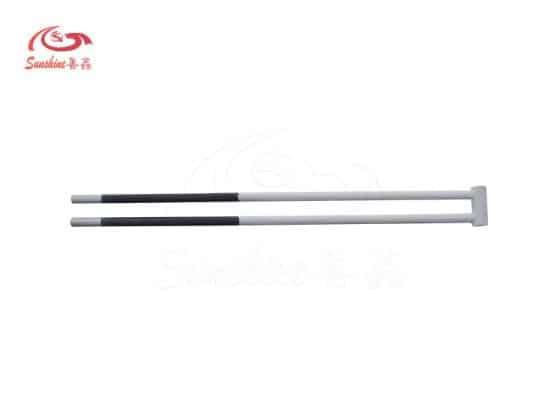
In the actual production environment, several harmful volatiles possibly exist in some furnaces meanwhile, and even some harmless volatiles become harmful after mixed with some other volatiles, thereby affecting the service life of heater.
In order to extend the service life of heater in different atmospheres, we developed various coating to protect the SiC structure of heater to prevent rapid aging, the coatings we have mainly are:
A Coating sic heater elements,
B Coating sic heater elements,
D Coating(Alkali-resistant) sic heater elements
Specification for alkali resistant coating SiC heater:
- Coating type: D
- Appearance:white grey, without luster.
- Tube Diameter:8mm to 65mm
- Voltage:110-480v
- Working temperature:up to 1450
Advantages of Alkali Resistant Coating of SiC heater
Alkali-resistant Coating is mainly used in atmosphere of alkali metal, under this atmosphere, alkali metal is easy to congeal on surface of heater and react with SiC on surface, thereby accelerate the aging of heater.Alkali resistant coating SiC heater will protect the heater body and prolong the service life of it.
How to choose the coating of SiC heater?
Since different coatings have different effects in different atmospheres, it’s necessary to proceed the small batch tests against the specific problem in order to find out the optimum plan and select the best coating.
After years of testing, we have developed a variety of sic heaters elements for different environments.
A Coating(Resistant to Vapor and Moisture),
B Coating(Resistant to Nitrogen gas and ammonia),
D Coating(Alkali-resistant)
Application of Alkali-resistant Coating SiC heater:
The alkali&alkaline metal oxide will react with SiC at about 1300℃ and genetate silicate, which calls alkali-chemical corrosion,and can influence the glowing of element evidently.
Atmosphere | Effect | Solution | Recommend Coat |
Vapor and Moisture | Service life shortened 20% than in dry air | New furnace or old furnaces not work long time, to dry at low temperature completely and then heat up | A coat |
Nitrogen gas | Above 1400℃, nitrogen will react with SiC to form silicon nitride, elements will become fragile and service life shortened. The effect by d&ew point is same as H2 | The recommended furnace temperature not higher than 1300℃, surface loading as low as possible | B coat |
Hydrogen | The mechanical strength decreasing when elements temperature exceeds 1350℃, and also service life much depends on intensity of moisture. | Operation temperature lower than 1300℃, surface loading less than 5W/ CM² | |
Ammonia | Same as hydrogen and nitrogen | Operation temperature lower than 1300℃, surface loading less than 5W/CM² | B coat |
Disassociated gas(Mixture of N2, CO, CO2, H2, CH4) | Carbon black from decomposed hydrocarbon on elements surface will cause elements rod loose. | Introducing air into furnace frequently to burn up additional Carbon. At side of furnace design, keep enough space between elements to prevent short circuit. | |
(S、S2) | Above 1300℃, surface of elements will be corroded and resistance increasing rapidly. | Keep elements temperature lower than 1300℃ | |
Vacuum | SiO2 protect film will not be formed, SiC decomposed itself and service life shortened. | Using in pressure over 0.13Pa and furnace temperature under 1100℃ | |
Others | Various substances from treated materials, such as Pb, Sb, alkali metal react with elements, which may shorten elements service life. | To get rid of these substances in advance, design gas outlet in furnace in order to decrease the effect. | D coat |
Which shape silicon-carbon heating elements can be added with alkali-resistant coating?
Coating is an additional process for silicon-carbon heating elements, and all the shapes of silicon-carbon rods that can be coated as following:
DB type silicon carbide heater rod
ED type sic heating elements
M type Globar silicon carbide heating element
SG type SiC heating elements(single spiral)
SGR type Double Spiral Silicon Carbide Heating Element Max temperature 1625 ℃
Slot type sic heating element
They are all called alkali resistant coating SiC heater after D coating.
Customers can choose alkali resistant coating SiC heater according to your own furnace operating environment.