MoSi2 electric heating element is a resistance heating element made of molybdenum disilicide, which has high-temperature and oxidation resistance. It is often used in different kinds of high-temperature equipment.
The layout of molybdenum disilicide heating elements means the interval, shape and installation way of the heating elements inside the furnace, to guarantee the heating performance and lifespan.
Attention for installation and layout of molybdenum disilicide heating elements
The molybdenum disilicide heating element has soft plasticity at high temperature, and in general, the working current is larger, which causes the hot end to bulge outward under the action of magnetic force. If the installation is not set properly, it will cause the adjacent two heating bodies to touch each other, or the heating body to touch the furnace wall, so attention should be paid when designing the electric furnace and the electric heating element.
The commonly used molybdenum disilicide heating elements are mostly single U-shaped or multi-U-shaped combinations. The current flowing in the element generates electromagnetic force, which causes repulsive force between the two sides of the U-shape, leading to an increase in the distance (center distance) A between the elements after being energized and when the heating zone reaches the softening temperature. As follows:
The heating part (hot end) of the new unused U-shaped element has two legs that are neatly parallel, but the used element, especially after a long time of use, will show obvious bow-shaped deformation at the hot end, which is actually a direct manifestation of the influence of electromagnetic force on the element.
We recommend that users reduce the surface load of the molybdenum silicide heating element as much as possible during the design and use process. According to the actual situation of the electric furnace, try to arrange the heating element as many as possible at the design stage, and choose a larger diameter for the hot end length as much as possible.
Our 1700 Grade molybdenum disilicide heating element is recommended to have a surface load of no more than 13.5w/cm2 at a furnace temperature of 1300 degrees. For 1800 Grade molybdenum disilicide heating element, the surface load is less than 11.5w/cm2 at a furnace temperature of 1600 degrees.1850 Grade molybdenum disilicide heating element has a surface load of less than l2w /cm2 at a furnace temperature of 1720 degrees. Under the conditions permitted, a lower surface load will effectively improve the service life of the heating element
Reduce the difference between the heating element and the furnace temperature, and better ensure the uniformity of the electric furnace heat field.
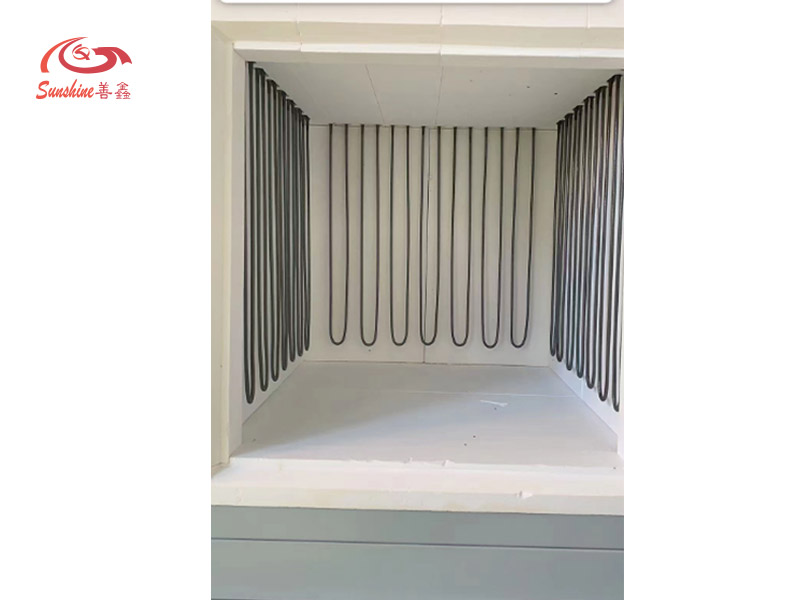