What is a coating silicon carbide heating element?
A coating silicon carbide heating element is an antioxidant coating heating element.
A coating can delay the oxidation of silicon carbon rods and extend the life of the heating element.
Why you need a coating?
Though the element will be oxidized very slowly in course of application,it also will make the resistance increased following long time application, this phenomenon calls aging.
In order to lower the aging speed and extend the service life of heater in different atmospheres, we use special technology to coat a protect film on the surface of heating element in the course of production.A coating silicon carbide heating element can effectively block water vapor, nitrogen, hydrogen, alkaline gas, metal oxide and other harmful gas volatiles, and effectively reduce the erosion of harmful gas volatiles on silicon carbon rods.
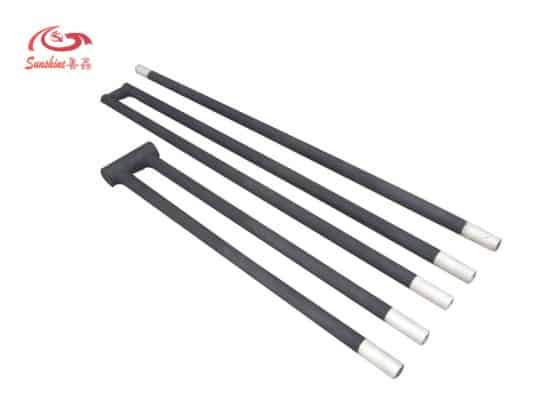
What are the common coatings for silicon carbon heating element?
Flexure strength | 50MPa |
Porosity | 23% |
Heat conductivity (hot end) | 12-18W/m+℃ at 1000℃ |
Specific heat | 1.0 kj/kg+℃ at 25℃-1300℃ |
Specific resistance (hot end) | 0.08Ω cm at 1000℃ |
The coefficient of thermal expansion | 4.5X10-6 |
Voltage | 110 – 480v |
SiC Content | Above 99% |
Material | Silicon carbide, Silicon Carbide (SiC) |
Appearance | black, with glassy luster |
Working temperature | Up to 1500 ℃ |
Volume density | 2.6-2.8g/cm3 |
Application | Industrial Heating Parts |
After-sales Service Provided | Overseas service center available |
Brand Name | SUNSHINE |
The coatings mainly include A Coating, B Coating, D Coating, which can enhance the Antioxidant property of element evidently and lengthen the service life.Since different coatings have different effects in different atmospheres, it’s necessary to choose the best coating against the specific problem.
Video
Coating type: A
Appearance: black, with glassy luster
Application:The silicon carbide(sic) heating element without anti-oxidation and waterproof coating has a high porosity, and the external oxygen not only reacts with the silicon carbide surface, but also directly enters through the opening pore and reacts with the inner silicon carbide.
Although silicon carbide heating elements in the process of use can also generate a layer of SIO2 protective film, the generated protective film is not continuous, not dense, in the process of use by temperature change or mechanical impact is easy to produce small cracks and spalling, and the self-healing ability is poor, provides a channel for the rapid diffusion of oxygen, resulting in poor oxidation resistance of the element and short service life.
When the silicon carbide(sic) heating element is coated with anti-oxidation coating, the surface of the self-healing oxidation, gradually forma certain amount of SiO2 rich dense glass phase protective film evenly spread on the SiC heating element surface, and bonded with the element surface close firmly, effectively shield the entry of external oxygen, make the oxidation reaction of the matrix is fully inhibited and protect the SiC electric heating elements.
A coating silicon carbide heating element(waterproof) can protect the film on the surface of heating element.
The application of A coating silicon carbide heating element in the furnaces with oxidization and vapor, its service life improves more than 30%.
Atmosphere | Effect | Solution | RecommendCoat |
Vapor and Moisture | Service life shortened 20% than in dry air | New furnace or old furnaces not work long time, to dry at low temperature completely and then heat up | A coating (anti-oxidation and waterproof coating) |
Nitrogen gas | Above 1400℃, nitrogen will react with SiC to form silicon nitride, elements will become fragile and service life shortened. The effect by dew point is same as H2 | The recommended furnace temperature not higher than 1300℃, surface loading as low as possible | B coating |
Hydrogen | The mechanical strength decreasing when elements temperature exceeds 1350℃, and also service life much depends on intensity of moisture. | Operation temperature lower than 1300℃, surface loading less than 5W/ CM2 | |
Ammonia | Same as hydrogen and nitrogen | Operation temperature lower than 1300℃, surface loading less than 5W/ CM2 | B coating |
Disassociated gas(Mixture of N2,CO,CO2,H2,CH4) | Carbon black from decomposed hydrocarbon on elements surface will cause elements rod loose. | Introducing air into furnace frequently to burn up additional Carbon. At side of furnace design, keep enough space between elements to prevent short circuit. | |
(S、S2) | Above 1300℃, surface of elements will be corroded and resistance increasing rapidly. | Keep elements temperature lower than 1300℃ | |
Vacuum | SiO2 protect film will not be formed, SiC decomposed itself and service life shortened. | Using in pressure over 0.13Pa and furnace temperature under 1100℃ | |
Others | Various substances from treated materials, such as Pb, Sb, alkali metal react with elements, which may shorten elements service life. | To get rid of these substances in advance, design gas outlet in furnace in order to decrease the effect. | D coating |
The advantage of A coating silicon carbide heating element
The oxidizing effect of oxygen and water steam on rod body is prevented, and the service life of A coating silicon carbide heating element in the oxidizing furnace with water steam is increased by more than 30%.
Customers can choose A Coating Silicon carbide heating elements according to your own furnace operating environment.