The erosion of matched fixture to molybdenum disilicide heating element at high temperature is a common problem, which may lead to the shortening of the lifespan and the degradation of the performance of molybdenum disilicide heating elements.
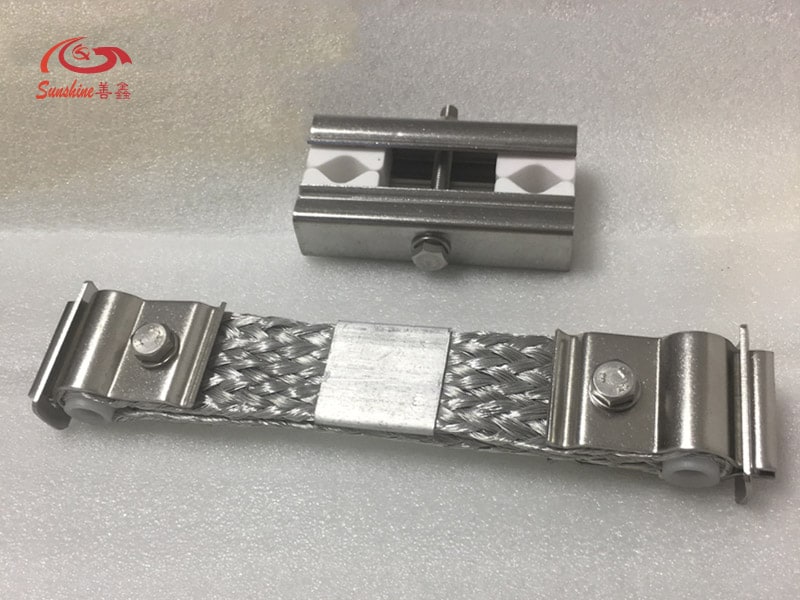
To solve this problem, there are several methods as follows:
- Choose suitable ceramic materials, reduce their thermal expansion coefficient and thermal conductivity, and decrease the thermal stress and thermal contact with molybdenum disilicide.
- Optimize the structure and shape of ceramic fixtures, increase the gap between them and silicon molybdenum rods, and avoid too tight or too loose clamping.
- Check and replace ceramic fixtures regularly, find and eliminate defects such as cracks, deformation, looseness, etc. in time.
- Control the heating temperature and time, avoid too high or too long heating, and reduce the oxidation and embrittlement of molybdenum disilicide heating elements.
- Apply a layer of anti-corrosion lubricant or protective coating between ceramic fixtures and molybdenum disilicide heating element, such as boron nitride, alumina, etc., to reduce the friction and reaction between them.
- In the furnace design, try to keep the temperature of the top part of the furnace low.