Reaction sintering silicon carbide ceramics is also called Reaction Bonded Silicon Carbide (RBSiC/SiSiC).
Reaction sintered silicon carbide uses a certain particle size distribution of silicon carbide (generally 1~10μm) and carbon mixed and formed green body, and then reacts with silicon at high temperature, part of silicon and carbon react to form SiC and combine with the original SiC in the green body, to achieve the sintering purpose. There are two methods of silicon infiltration, one is to reach the melting temperature of silicon (1450-1470℃), produce the liquid phase of silicon, through the capillary action, silicon directly enters the green body and reacts with carbon to form silicon carbide, to achieve sintering; the other is to exceed the melting temperature of silicon, produce silicon vapor, and infiltrate the green body with silicon vapor to achieve sintering.
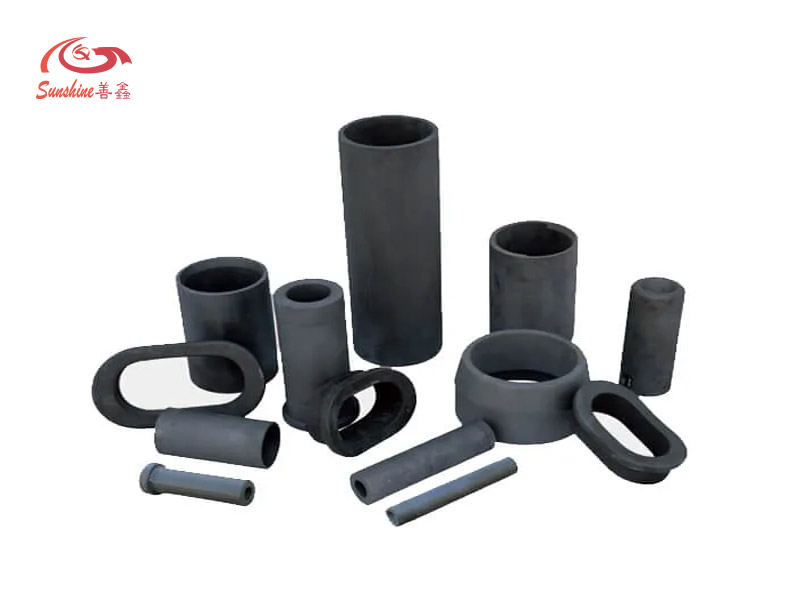
It is worth noting that the use temperature range of reaction sintered silicon carbide is limited by the free Si content in the material, usually within 1400℃, if above 1400℃, the strength of the material will rapidly decrease with the melting of free Si. The first method of sintering generally leaves more free silicon, usually reaching 10% to 15%, sometimes more than 15%, which will bring adverse effects to the product performance. Using gas phase method to infiltrate silicon, because the reserved pores of the green body can be as few as possible, the free silicon content after sintering can be reduced to below 10%, some process control can be reduced to below 8%, the product performance is greatly improved.
SiC powder + C powder + binder mixing → forming → drying → atmosphere protection degumming → high temperature Si infiltration → subsequent processing.
The previous process also illustrates a point, the silicon carbide ceramics prepared by this process will have more or less Si residue (up to more than 15%, less than about 8%), so, the ceramics made by this process are not single-phase silicon carbide ceramics, strictly speaking, it is “silicon + silicon carbide” composite material: so this RBSiC also has SiSiC (silicon carbide composite material) name.
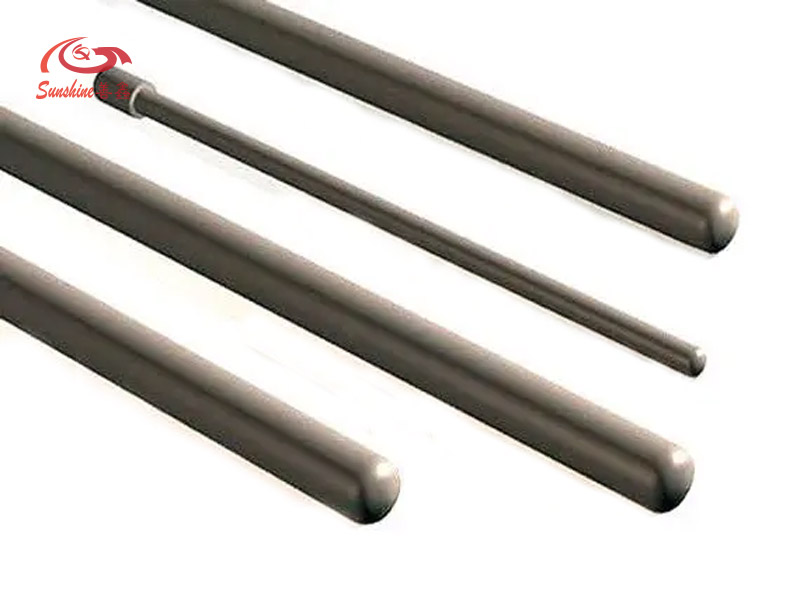
The process characteristics and applications of Reaction sintered silicon carbide ceramics
The advantages of reaction sintered silicon carbide are low sintering temperature, low production cost, high degree of material densification, carbon and silicon carbide skeleton can be pre-turned into any shape, and the shrinkage of the green body during sintering is only within 3%, which is conducive to the product size control, greatly reducing the grinding amount of the finished product, especially suitable for the preparation of large size complex shape structural parts.
Therefore, in industrial production, the output is large, mainly used for furnace materials, crucibles and cassettes, etc. Because silicon carbide has low thermal expansion coefficient and high elastic modulus, reaction sintered silicon carbide also becomes the ideal material for space reflector. The most famous reaction sintered silicon carbide production company in the world is Refel company in the UK, which has been widely used to make high temperature exchangers. Japan’s Asahi Glass Company introduced this technology and made 0.5~1m long heat exchange tubes and other products.
With the increase of chip size and heat treatment temperature, higher requirements are put forward for the parts in the process. Using high-purity silicon carbide powder and high-purity silicon, high-purity silicon carbide parts containing partial silicon phase can be made, gradually replacing quartz glass parts in the support fixtures of electron tubes and semiconductor chip manufacturing equipment.
The disadvantages of Reaction sintering silicon carbide ceramics
As mentioned earlier, this process determines that there is always free silicon residue in the green body after sintering, which will affect the application of the product in the future, the strength of the sintered body is not as good as other process products, the wear resistance decreases, the most important thing is that free silicon can not resist alkaline and hydrofluoric acid and other strong acid medium corrosion, so its use is limited. In addition, the high temperature strength is also affected by free silicon, the general use temperature is limited to below 1350-1400℃.