General description
High alumina brick is a kind of refractory material, the main component of this refractory brick is Al2O3 alumina, and is of vital importance in many fire bricks due to its high melting point.
Alumina is one of the most chemically stable oxides, and it offers excellent hardness, strength and spalling resistance.
Alumina refractories have the advantages of a high resistance in oxidizing and reducing atmosphere and is extensively used in heat processing industries.
The content of aluminum oxide (Al2O3) in high alumina bricks is higher than 48%. How much high alumina content is bigger, that much refractoriness of refractory brick is better.

High alumina brick are suitable for lining furnace operating up to 1850°C.
High Alumina bricks have great features like high temperature performance, great corrosion and wear resistance, high bulk density, low iron content, etc.
Classification of high alumina bricks
Depending on the Al2O3 content, high alumina bricks are usually classified into following grades:
Product Name/Item | Special Gradehigh-alumina brick | Grade Ihigh-alumina brick | Grade IIhigh-alumina brick | Grade IIIhigh-alumina brick |
Al2O3 content | ≥80% | 75%~80% | 60% ~ 75% | 55%~ 60% |
Fe2O3< | 2.0 | 2.5 | 2.5 | 2.6 |
Bulk Density | 2.6 | 2.5 | 2.4 | 2.3 |
compression strength | 80 | 70 | 60 | 50 |
Refractoriness under load | 1550 | 1510℃ | 1460℃ | 1420℃ |
Temperatura de trabalho | 1500℃ | 1500℃ | 1440℃ | 1350°C |
Refractoriness | 1790℃ | 1790℃ | 1790℃ | 1790℃ |
porosidade | 21 | 22 | 23 | 24 |
linear change rate | -0.27 | -0.37 | -0.4 | -0.4 |
According to the shape and size of high alumina bricks can be knife type, axe type, wedge high alumina brick, high alumina arch foot brick, high alumina anchor brick and so on.
Especificação
Standard sizes of High Alumina Bricks are:
- Standard bricks: 9” x 4.5” x 3” ; 9”x4.5”x2” ; 9”x4.5”x1.5” ; 9”x4.5”x1”
- Side Taper (Side Arch): 9” x 4.5” x 3”/2.75” ; 9” x 4.5”x3”/2.5” ; 9”x4.5”x3”/2”
- End taper (End Arch): 9”x4.5”x3”/2.75” ; 9” x 4.5”x3”/2.5” ; 9”x4.5”x3
Customized shapes can also be made as per the requirement.
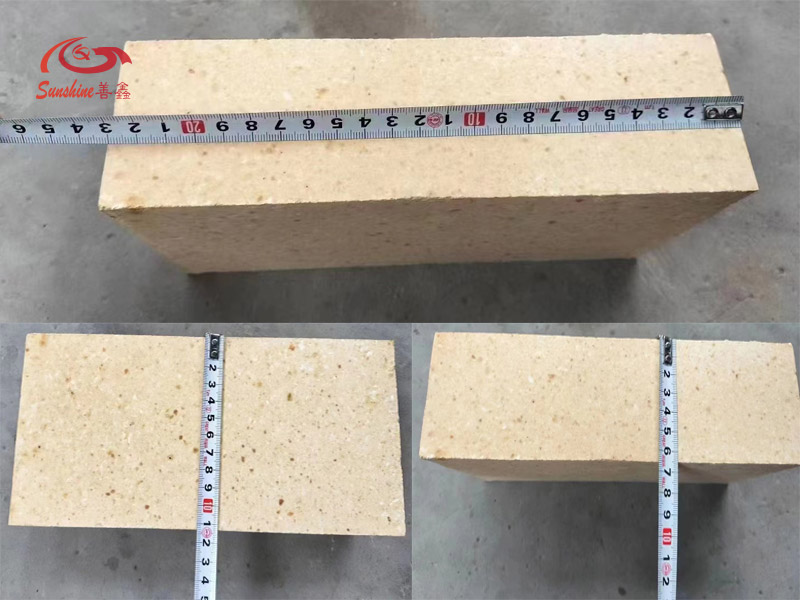
Depending on the Al2O3 content, high alumina bricks are usually classified into following grades:
- High alumina brick 45 – 54%
- High alumina brick 55 – 65%
- High alumina brick 66 – 74%
- High alumina brick 75 – 85%
- High alumina brick > 85
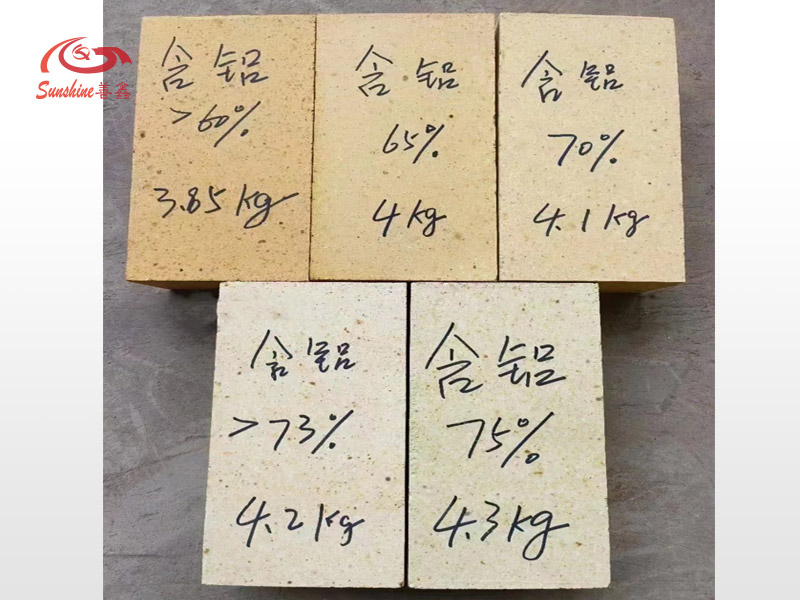
High Alumina Brick Properties
1.High Alumina Bricks belong to advanced refractory materials. They have higher refractoriness reaching up to 1750~1790℃ than fire clay bricks and semi-silica bricks.
2.High Alumina Bricks have higher refractoriness under load than fireclay bricks because that high alumina bricks have higher Al2O3 content and low impurities which forming little fusible vitreum body. But because mullite crystal does not form network structure, their refractoriness under load is lower than silica bricks.
3.High Alumina Bricks have more Al2O3 content and belong to neutral refractory materials that can resist acid and basic slag erosion. And as they also contain SiO2 content, high alumina brick can better resist acid slag erosion than basic slag erosion.
High Alumina Brick Application
High Alumina Bricks are mainly used to build blast furnace, hot blast stove, top of electric furnace, air furnace, reverberatory furnace and lining of rotary kiln.
High Alumina Brick is also can be used as checker bricks of heat accumulating type, chock plug for gating system, nozzle brick and so on.
It can also be used in the following environments
- Glass tanks
- Ceramic kilns
- Cement kilns
- Enamel kilns
- Steel refining furnaces
Advantages of high alumina bricks
- Refractoriness
The refractoriness of high alumina bricks is higher than that of clay, semi-silica bricks and other refractory materials we commonly use, up to 1750~1790 °C. It is a high-performance refractory material. Usually, refractory bricks with higher alumina content have better refractory performance. - Load softening temperature
Because the alumina content in high alumina bricks is relatively high and there are fewer impurities, the glass body that is easier to melt becomes less, so its load softening temperature is relatively high. - Thermal conductivity
High alumina bricks have excellent thermal conductivity, because there are fewer glass components with poor thermal conductivity inside high-alumina bricks, and the content of stone and corundum crystals with excellent thermal conductivity is relatively high, so the thermal conductivity is relatively good. - Resistência ao choque térmico
The thermal shock resistance of high-alumina bricks is between clay and siliceous products, mainly because the mullite content in high-alumina bricks is relatively high, which improves the particle structure of products and improves the thermal shock resistance of high-alumina bricks. stability. - Slag resistance
Because the alumina content in the high alumina brick is relatively large, it has a certain resistance to the erosion of acid slag and alkaline slag. At the same time, the slag resistance of high-alumina products also has a certain influence on the stability of products in slag. Usually, after high-temperature firing, the slag resistance of high-alumina bricks with fewer pores is better.
High alumina bricks VS fireclay bricks
Bricks with aluminum oxide contained more than 55% are high alumina bricks while those lower than 55% are fire clay bricks.
The main chemical composition of alumina bricks is aluminum oxide (Al2O3). (Chinese standard of high alumina bricks is more than 48% of Al2O3, but the III class high alumina bricks should have no less than 55% Al2O3.)
Type of bricks | High Alumina Brick | Fire Clay Brick |
Aluminum Oxide (%) | ≥55 | 30~55 |
Bulk Density (g/cm3) | 2.3~2.5g/cm3 | 1.8~2.3g/cm3 |
Refractoriness (℃) | 1690~1730 | 1750~1790 |
Sunshine element supply high quality High Alumina Bricks at reasonable prices and our experts and team can provide excellent services to our clients. Our Alumina Bricks are best suited for industrial use as they can survive any temperature and pressure.